A corrosão é um problema persistente e complexo enfrentado pela indústria ferroviária, afetando diretamente a segurança, a eficiência e a economia das locomotivas. Esses veículos operam em condições ambientais severas, incluindo alta umidade, poluição atmosférica e exposição a sais e contaminantes industriais, que aceleram o processo corrosivo e comprometem a integridade dos componentes metálicos.
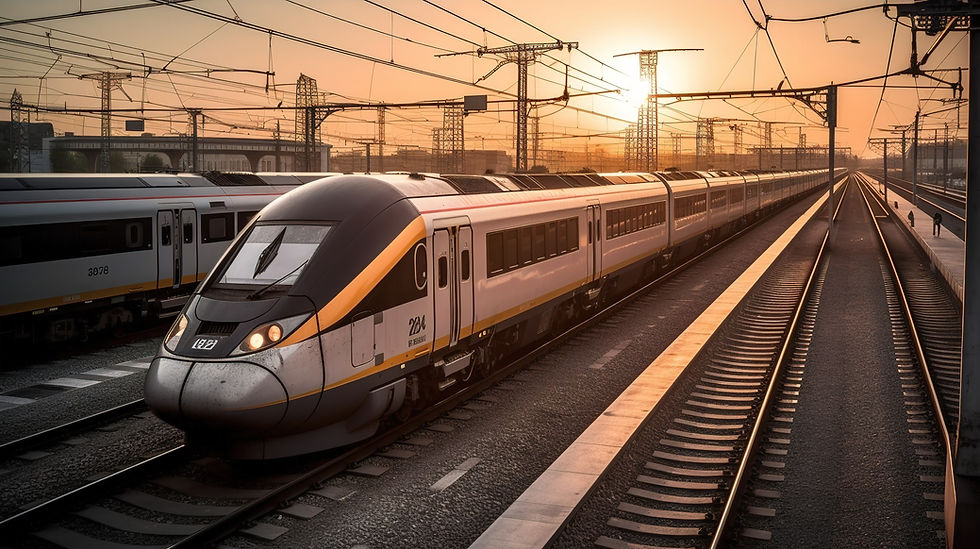
Entre os tipos de corrosão que mais afetam as locomotivas, destacam-se a corrosão galvânica e a corrosão por fadiga. A corrosão galvânica ocorre quando metais diferentes entram em contato em um ambiente eletrolítico, resultando no desgaste acelerado de um dos metais. Em locomotivas, isso é especialmente problemático em ambientes costeiros ou industriais, onde a umidade e a salinidade intensificam a corrosão. Já a corrosão por fadiga combina estresse mecânico com ataque químico, gerando rachaduras e falhas estruturais em componentes críticos como chassis e sistemas de suspensão. Esses problemas não apenas comprometem a segurança, mas também podem levar a falhas graves durante a operação, não esquecendo de citar a corrosão em equipamentos hibernados.
Os impactos financeiros e operacionais da corrosão são substanciais. Estudos indicam que o custo anual de manutenção ferroviária na Europa chega a cerca de €15 bilhões (BCG Global). Este gasto inclui a substituição prematura de peças corroídas, a necessidade de repintura e a perda de eficiência mecânica. Além disso, a corrosão pode causar paradas inesperadas, afetando a produtividade e resultando em perdas financeiras. Falhas em componentes críticos, como sistemas de freios e chassis, podem levar a acidentes graves, com consequências financeiras e humanas devastadoras.
Um exemplo notável dos riscos associados à corrosão ocorreu em 2013, com o descarrilamento do trem da Metro-North Railroad em Nova York, causado por falhas em trilhos corroídos, resultando em mais de 70 feridos. Este incidente sublinha a importância de adotar medidas preventivas eficazes para evitar tais consequências.
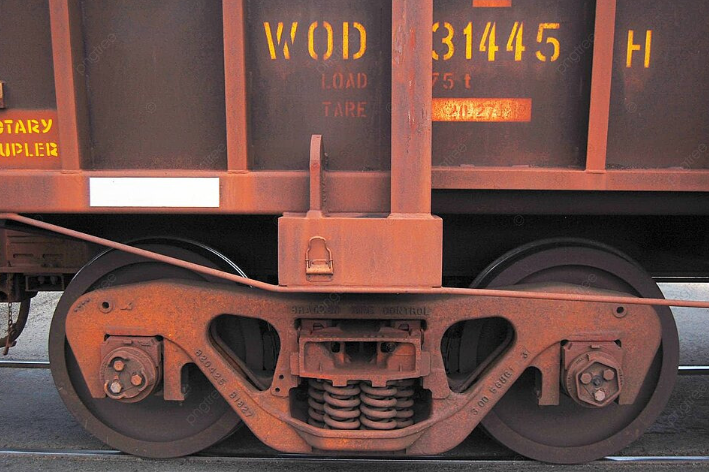
Para enfrentar esses desafios, a indústria ferroviária deve adotar uma abordagem proativa e utilizar soluções avançadas. Os revestimentos anticorrosivos especializados, como os oferecidos pela Tectyl, são fundamentais para proteger os componentes das locomotivas. Estes revestimentos criam uma barreira protetora eficaz contra umidade, salinidade e contaminantes industriais. Por exemplo, revestimentos baseados em cera ou resina são altamente eficazes em ambientes marítimos, onde a combinação de sal e umidade pode acelerar a corrosão. Esses revestimentos são aplicados em áreas críticas, como chassis e eixos, prolongando a vida útil dos componentes e reduzindo a necessidade de manutenção corretiva.
Além dos revestimentos, tecnologias avançadas de monitoramento desempenham um papel crucial na prevenção de falhas estruturais. Sensores de corrosão, como os eletroquímicos e ultrassônicos, fornecem dados em tempo real sobre a condição dos componentes. Sensores eletroquímicos medem a corrosão ao monitorar mudanças na resistência elétrica de um material, enquanto sensores ultrassônicos detectam variações na espessura do metal, sinalizando possíveis áreas de corrosão. A integração dessas tecnologias permite a detecção precoce de problemas, possibilitando ações corretivas antes que ocorram falhas graves.
Outra solução eficaz é a implementação de um programa de manutenção preventiva e programada. Inspeções regulares e planejadas, como inspeções visuais e testes de integridade estrutural, ajudam a identificar e corrigir problemas antes que se tornem críticos. Adicionalmente, a utilização de técnicas de proteção catódica, como ânodos de sacrifício, pode prevenir a corrosão em componentes metálicos expostos. Esses ânodos corroem-se no lugar do metal principal, oferecendo uma proteção adicional.

No campo das soluções inovadoras, a aplicação de revestimentos nanotecnológicos está emergindo como uma alternativa promissora. Esses revestimentos utilizam partículas de tamanho nanométrico para criar uma camada extremamente fina e resistente à corrosão, proporcionando uma proteção superior e duradoura. A nanotecnologia oferece uma adesão mais forte ao substrato e maior resistência ao desgaste e aos agentes corrosivos, tornando-se uma solução ideal para ambientes ferroviários severos.
Finalmente, a educação e o treinamento contínuo das equipes de manutenção são essenciais para a eficácia dessas soluções. Profissionais capacitados na identificação de sinais de corrosão e na aplicação adequada de tecnologias de proteção garantem que as locomotivas permaneçam seguras e operacionais. Programas de treinamento que abordam as melhores práticas para aplicação de revestimentos e utilização de tecnologias de monitoramento contribuem para a prevenção de problemas e para a manutenção da integridade das locomotivas.
Investir em práticas de proteção anticorrosiva e em tecnologias avançadas é crucial para garantir a segurança e a eficiência das operações ferroviárias. Ao adotar uma abordagem proativa, as empresas ferroviárias podem proteger seus ativos, reduzir os custos de manutenção e minimizar os riscos de acidentes graves. A prevenção e a inovação são fundamentais para manter a integridade das locomotivas e assegurar a continuidade segura das operações ferroviárias.
---------------------------------------
Corrosion is a persistent and complex issue faced by the railway industry, directly affecting the safety, efficiency, and economics of locomotives. These vehicles operate under severe environmental conditions, including high humidity, atmospheric pollution, and exposure to salts and industrial contaminants, which accelerate the corrosive process and compromise the integrity of metal components.
Among the types of corrosion that most impact locomotives, galvanic corrosion and fatigue corrosion are particularly notable. Galvanic corrosion occurs when dissimilar metals come into contact in an electrolytic environment, resulting in the accelerated wear of one of the metals. In locomotives, this is especially problematic in coastal or industrial environments, where moisture and salinity intensify corrosion. Fatigue corrosion, on the other hand, combines mechanical stress with chemical attack, leading to cracks and structural failures in critical components such as chassis and suspension systems. These issues not only jeopardize safety but can also lead to severe operational failures, including those affecting hibernated equipment.
The financial and operational impacts of corrosion are substantial. Studies indicate that the annual cost of railway maintenance in Europe reaches approximately €15 billion (BCG Global). This expense includes the premature replacement of corroded parts, the need for repainting, and the loss of mechanical efficiency. Additionally, corrosion can cause unexpected stoppages, affecting productivity and resulting in financial losses. Failures in critical components, such as braking systems and chassis, can lead to serious accidents with devastating financial and human consequences. A notable example of the risks associated with corrosion occurred in 2013 with the derailment of the Metro-North Railroad train in New York, caused by failures in corroded tracks, resulting in over 70 injuries. This incident underscores the importance of implementing effective preventive measures to avoid such outcomes.
To address these challenges, the railway industry must adopt a proactive approach and utilize advanced solutions. Specialized anticorrosive coatings, such as those offered by Tectyl, are essential for protecting locomotive components. These coatings create an effective protective barrier against moisture, salinity, and industrial contaminants. For example, wax- or resin-based coatings are highly effective in maritime environments, where the combination of salt and moisture can accelerate corrosion. These coatings are applied to critical areas, such as chassis and axles, extending component life and reducing the need for corrective maintenance.
In addition to coatings, advanced monitoring technologies play a crucial role in preventing structural failures. Corrosion sensors, such as electrochemical and ultrasonic sensors, provide real-time data on component condition. Electrochemical sensors measure corrosion by monitoring changes in a material's electrical resistance, while ultrasonic sensors detect variations in metal thickness, signaling potential corrosion areas. Integrating these technologies allows for early problem detection, enabling corrective actions before severe failures occur.
Another effective solution is implementing a preventive and scheduled maintenance program. Regular and planned inspections, such as visual inspections and structural integrity tests, help identify and address issues before they become critical. Additionally, using cathodic protection techniques, such as sacrificial anodes, can prevent corrosion in exposed metal components. These anodes corrode in place of the main metal, providing additional protection.
In the realm of innovative solutions, the application of nanotechnological coatings is emerging as a promising alternative. These coatings use nanoparticles to create an extremely thin and corrosion-resistant layer, offering superior and long-lasting protection. Nanotechnology provides stronger adhesion to the substrate and greater resistance to wear and corrosive agents, making it an ideal solution for harsh railway environments.
Finally, ongoing education and training for maintenance teams are essential for the effectiveness of these solutions. Skilled professionals in identifying corrosion signs and applying protective technologies ensure that locomotives remain safe and operational. Training programs addressing best practices for coating application and monitoring technologies contribute to problem prevention and the maintenance of locomotive integrity.
Investing in anticorrosive protection practices and advanced technologies is crucial for ensuring the safety and efficiency of railway operations. By adopting a proactive approach, railway companies can protect their assets, reduce maintenance costs, and minimize the risks of serious accidents. Prevention and innovation are key to maintaining locomotive integrity and ensuring the safe continuity of railway operations.
Comments